6. 3D models and copies
A 3D model is a model; a representation, and not a copy. The function and materiality of the original must be conveyed through other media. However, 3D models can be used to both tactilely and visually reinforce parts or the whole of the original and make them more accessible.
3D printing technology is based in and has its main applications in the field of making manufacturing industry models and prototypes. Its strength lies in being able to produce small series and individual copies. It is easy to make changes to the digital object and make quick test prints.
“In general, I would say that 3D printing still focuses on prototypes and exhibition objects. Making end-use objects which must withstand wear and tear over time is harder, but the technology is improving rapidly and new materials are introduced all the time.”
Quote: Martin Hansell at Arkitektkopia AB
A 3D model is not a copy
3D printing is not a suitable technique for copying artefacts which are to be touched, handled, and give a fair picture of the original object and its function. 3D print can reproduce the outer shape of the original, but not its functionality and materiality.
While 3D models can be processed and finished to have a surface, texture, and weight similar to the original, this is an expensive process which still cannot produce an authentic copy. It will still both feel and look like it is “just plastic”. Treated surfaces are also sensitive to wear and tear, even during careful handling, and plaster composite colour prints are very brittle. Certain types of objects, such as metal objects with soldered decorations and wooden, bone, and horn objects with fine, carved decorations, are also impossible to recreate in an acceptable way in 3D printing.
In most cases it is both faster, easier, cheaper, and better from an educational standpoint to have a craftsman produce a copy of the object in the original material, such as wood or metal using the correct technique, than creating and printing a digital 3D model. A copy made from authentic materials will also withstand the wear and tear of daily handling.
When making a copy with traditional craftsmanship, the work process itself becomes part of the object’s educational content. The film below shows how a copy of a rock carving from Nämforsen is done using stonecutting tools. The copy is made using a 3D scan of the original carving.
However, as part of the process of creating a craftsmanlike copy of an object, 3D models can function as valuable prototypes. They can also be used to produce moulds and wax models for lost-wax casting. For example, it would have been impossible to bring along and measure the original Alunda moose in the field, when creating a stone copy.
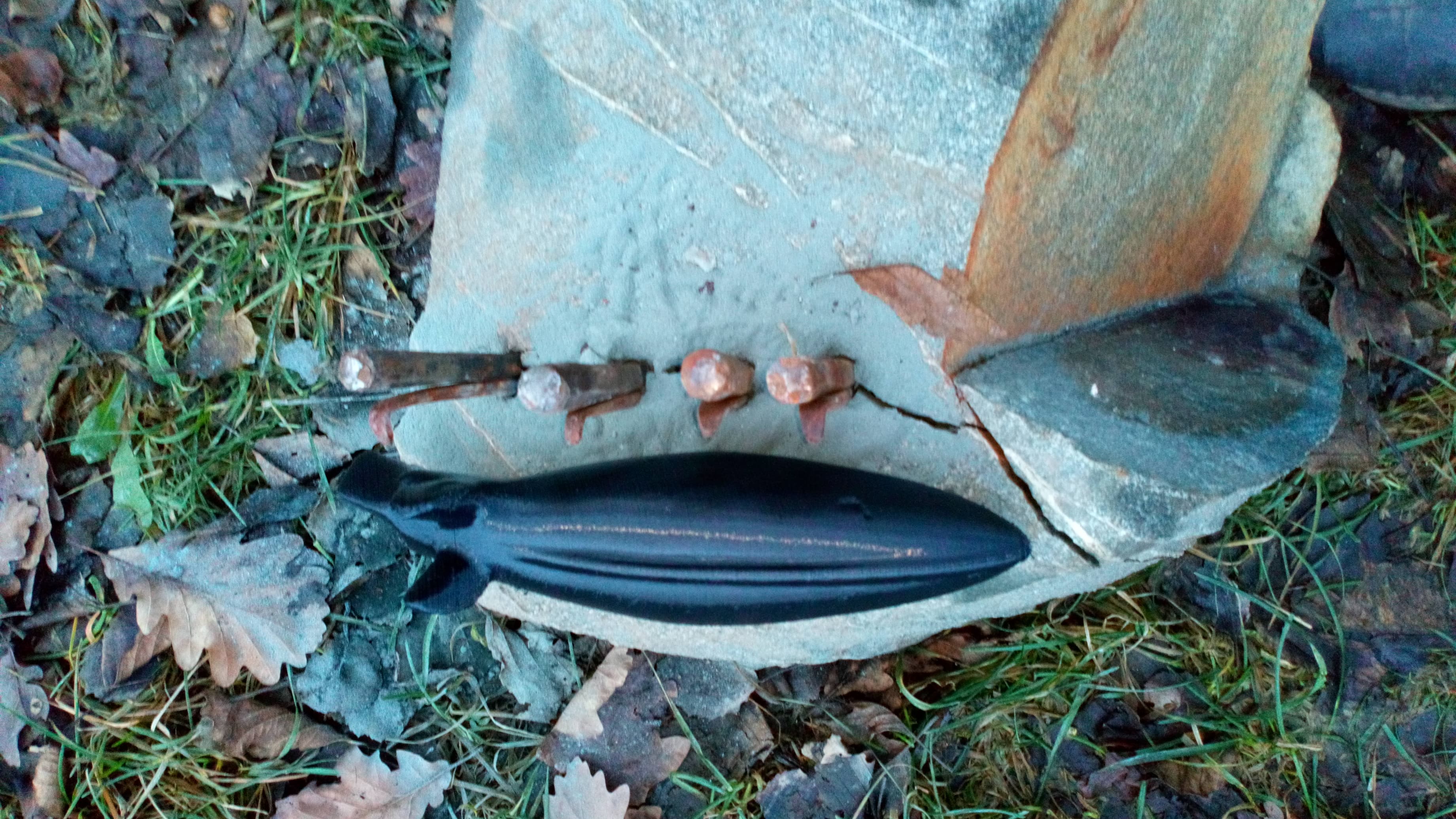
When making jewellery and other souvenirs for sale in museum shops, different sizes of the same object can easily be tried out in various scales. As metals such as silver and bronze can be 3D printed through selective laser sintering (SLS), smaller test runs of jewellery can also be produced. However, once you have found the desired size and material, larger scale production should be done using a most cost-efficient method.
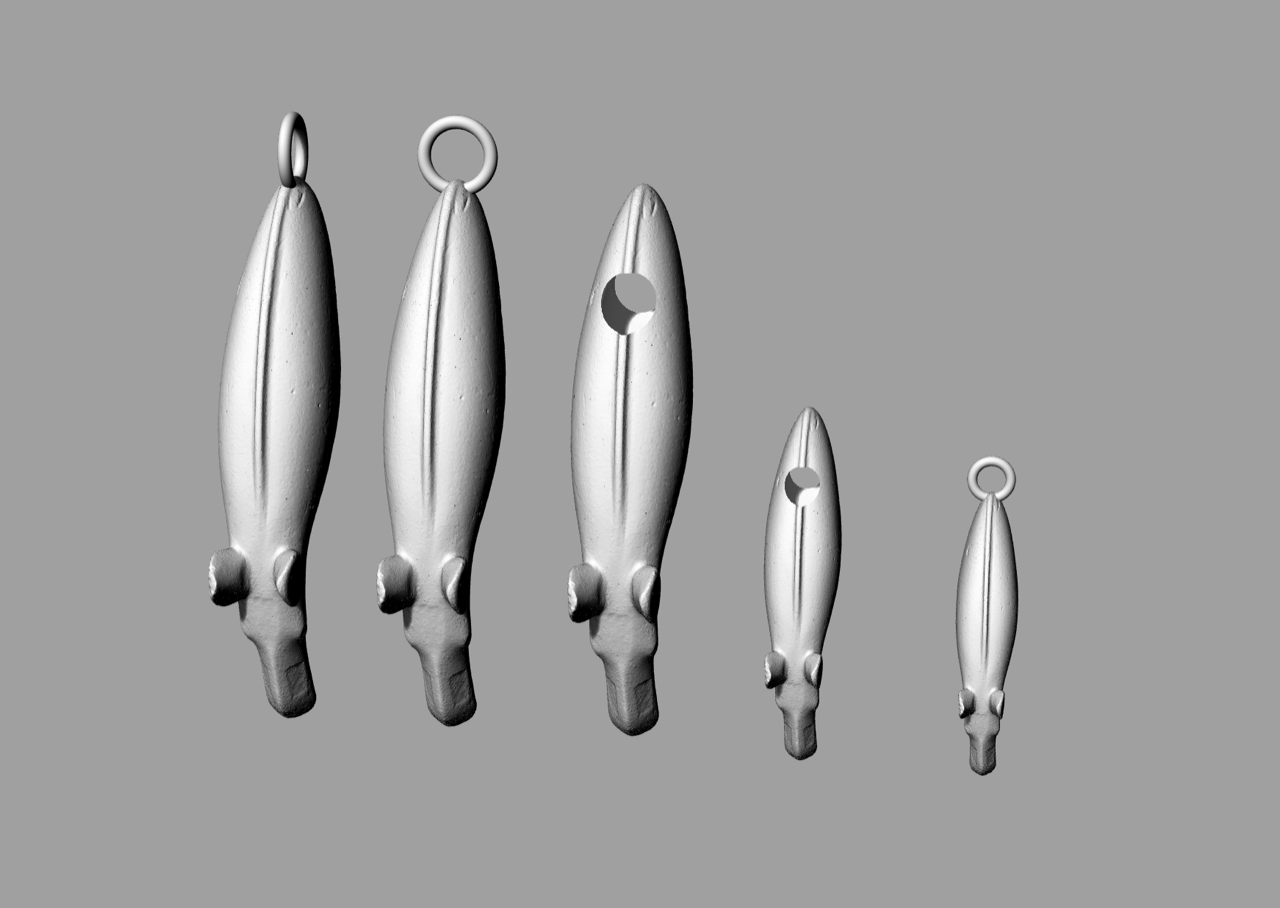